光学的仕様への理解
光学的仕様は、光学用の部品やシステムの設計や製造時の至る所で利用され、ある性能要件にどの程度十分に適合するのかを見極める判断材料となります。光学的仕様は、次にあげた2つの理由において重宝します。一つは、システム性能を決定する鍵となる特性の許容限界値を規定すること、そしてもう一つは、製造時にかかる時間やコストといったリソースの大きさを規定することです。
アンダースペックやオーバースペックに直面した光学システムは、不必要なリソースの浪費という結果を引き起こします。アンダースペックは、適切に規定された必要となる特性の全てを満足することができず、不十分な性能となります。オーバースペックは、システムが光学的あるいは機械的要件の変化に対して何も考慮されずに過剰に厳しい公差で作られてしまい、コストや製造難易度を高めてしまうことに繋がります。
光学的仕様を理解するために、まずはそれが意味していることを確認することが重要です。仕様の種類は非常に沢山ありますが、ここでは説明を簡略化するために、レンズやミラー、ウインドウの製品群に最も共通した製造や仕上げ、及び材料に関する仕様を取り上げます。フィルターや偏光板、プリズム、ビームスプリッター、回折格子、そしてファイバーオプティクスといった製品群にもこれらの仕様の多くが規定されているため、これを理解することでほぼ全ての光学製品の仕様を理解する上でのベースが出来上がることになります。
製造上の仕様
直径公差
円形光学部品の直径公差は、直径の大きさの許容範囲を表します。この製造公差は、光学部品を製造するメーカーの技量や対応力によって変わる場合があります。直径公差自体は光学部品の光学的性能に何の効果も与えませんが、ホルダー内に固定する際には考慮に入れなければならないとても重要な機械的公差です。例えば、光学レンズの実際の直径がその名目値から外れる場合、ホルダー内に固定したレンズの光軸と機械軸とが一致せずに、芯ずれを引き起こします (Figure 1)。直径に対する代表的な製造公差は、標準品質グレードで+0.00/-0.10mm、精密品質グレードで+0.00/-0.050mm、高品質グレードで+0.000/-0.010mmです。
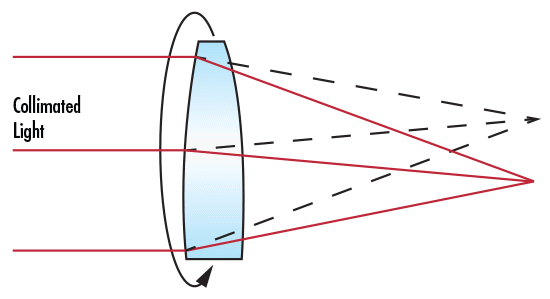
Figure 1: 芯ずれによるコリメート光の結像
中心厚公差
光学部品の中心厚公差は、特にレンズに関して言えば、中心部で測定される部品の基板厚さを表します。中心厚は、レンズの外周端部内の中心に当たる機械軸に対して測定されます。レンズの中心厚の大きさにバラツキがあると、光学性能に影響を及ぼす可能性が生じます。なぜなら、レンズの中心厚は、その曲率と併せて、レンズを通過する光線の光路長を決定付けるからです。中心厚に対する代表的な製造公差は、標準品質グレードで±0.20mm、精密品質グレードで±0.050mm、高品質グレードで±0.010mmです。
曲率半径
曲率半径の大きさは、光学部品の曲面部の頂点と曲面の中心点間の距離として定義されます。その大きさは、正の値、ゼロ、また負の値にもなり、対象面が凸面なのか、平面なのか、或いは凹面なのかでそれぞれ変わります。曲率半径の値を知ることで、レンズやミラーを通過する光線の光路長を決定付けるのと同時に、同面の光学的パワーも理解できるようになります。曲率半径に対する代表的な製造公差は、代表的なもので±0.5%ですが、精密アプリケーション用には±0.1%レベルにまで下がり、更には極度に高品質なニーズ向けには±0.01%になります。
偏芯
レンズのセンタリングや芯ずれとしても知られる偏芯は、ビームの変位量δで規定されます (下記公式 (1)を参照)。偏芯があると、ウェッジ角度 Wを単純な関係式から計算することができます (下記公式 (2)を参照)。レンズにおける偏芯の大きさは、レンズ機械軸の光軸からの物理的ずれを表します。レンズの機械軸は、単純にレンズの幾何学的中心軸を表し、レンズの外周部によって決められます。これに対して、レンズの光軸は光学面によって定義され、表裏二面ある光学面の曲率中心点同士を結んだ線になります。偏芯を試験するには、まずレンズをカップ状の固定治具内に圧力をかけてセットします。圧力をかけることで、レンズ第一面の曲率中心がカップの中心に自然と置かれ、カップの回転軸とも一致することになります (Figure 2)。回転軸にそってコリメート光を照射すると、カップ内に固定したレンズを通してその光がレンズの後側焦平面上で一点に集光します。この時、カップを回転することでレンズを回すと、レンズに偏芯がある場合は、後側焦平面上で半径Δの大きさの円の軌道を描きます (Figure 1)。
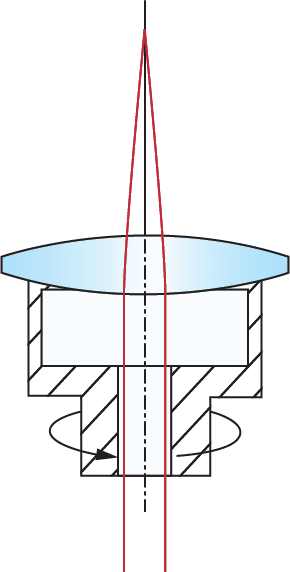
Figure 2: 偏芯に対する試験
ここで、Wはウェッジ角度 (分の単位で測定される場合も多い)、nは屈折率になります。
平行度
平行度は、光学部品の表裏二面が互いにどの程度平行であるかを表しています。ウインドウや偏光板といった平行平面がシステム性能上理想的な部品に対して規格化し、画像や光の品質を低下させる歪みを最小化するのに役立ちます。代表的な公差範囲は、5分から数秒までです。
角度公差
プリズムやビームスプリッターといった光学部品において、光学面間の角度構成の精度は、光学部品の性能にとって極めて重要です。この角度公差は、コリメート光を出射する光源を搭載するオートコリメーターシステムを用いて一般に測定されます。オートコリメーターを光学部品の被検対象面に向けて動かし、同面上で反射して戻ってくるフレネル反射光が入射するまで同機を回転させます。これにより、コリメート光が被検対象面に垂直入射で当たる状態なります。次に、オートコリメーター全体を次の被検対象面に向けて動かし、上述の作業を繰り返します。Figure 3は、オートコリメーターを用いて角度公差を測定する際の代表的なセットアップ例です。2つの測定位置間の角度的相違は、被検対象光学面二面間の公差を計算するのに用いられます。角度公差は、数分から数秒までの公差内で製造されます。
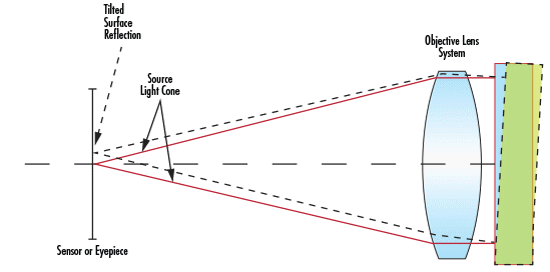
Figure 3: 角度公差を測定する際のオートコリメーターのセットアップ例
面取り
ガラスの角部は大変欠けやすく、部品としてそれを取り扱ったり、何かに固定する際には、その部分を保護しておくことが重要です。角部を保護する最も汎用的な方法は、ガラスの縁の部分を面取り加工することです。面取り加工は、端面保護として機能し、エッジ欠けの発生を防ぎます。面取り加工の大きさは、幅と角度を用いて表わされます (Figure 4)。

Figure 4: 光学レンズの面取り
面取りは、45°で裁断加工されるのが最も一般的で、その幅は光学部品の直径で決まります。マイクロレンズやマイクロプリズムといった直径3.0mm未満の光学部品の場合、素子の小ささゆえに加工時にエッジ欠けを引き起こしてしまう可能性があることから、通常は面取り加工されていません。一つ重要な点は、例えば、曲率半径が小さく、直径が曲率半径の0.85倍以上の条件に該当するレンズは、レンズの光学面と端部 (コバ面)によって形成される角度が大きくなることから、面取り加工が必要とされないことです。このケースに該当しない場合のレンズ直径別の最大面取り幅は、Table 1に紹介した通りです。
Table 1: 代表的な面取り加工 | |
---|---|
直径 | 最大面取り幅 |
3.00mm – 5.00mm | 0.1mm |
5.01mm – 25.4mm | 0.25mm |
25.41mm – 50.00mm | 0.3mm |
50.01mm – 75.00mm | 0.4mm |
有効径
有効径は、光学部品のスペック適用領域を直径かサイズで表わしたものです。有効径から外れる領域は、光学部品メーカーはそのスペックを保証しません。製造上の制約により、有効径を光学部品の直径や縦横寸法全体と全く同じにして生産するのは実質不可能です。レンズに対する代表的な有効径をTable 2に示します。
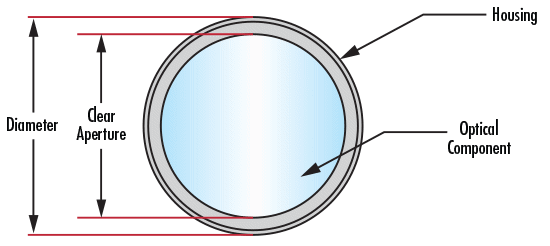
Figure 5: フィルターの有効径と直径を示した図
Table 2: 代表的な有効径の公差 | |
---|---|
直径 | 有効径 |
3.00mm – 10.00mm | 直径 x 0.9 (直径の中央90%) |
10.01mm - 50.00mm | 直径 – 1mm |
≥ 50.01mm | 直径 – 1.5mm |
外観上の仕様
表面品質
光学部品の表面品質スペックは、光学面の見た目を表したもので、スクラッチ (キズ)とディグ (ブツ)の2つの基準で規定されます。大抵の場合、これらの欠陥は単なる見かけ上の問題で、システムのスループットにわずかな損失と散乱光の増加を引き起こすことはありますが、システム性能に大きな影響を与えません。しかしながら、この影響がより大きくなるケースも存在します。例えば、対象光学面がシステムの像面上で焦点を結んでしまう場合は、光学面上の欠陥の像も結ばれてしまいます。またハイパワーの光が入射した時は、欠陥部によってエネルギーの一部が吸収され、結果的に光学部品に損傷を引き起こす場合もあります。表面品質に関する最も一般的に用いられている仕様は、MILの軍用規格、MIL-PRF-13830Bによって規定されたスクラッチ (キズ)とディグ (ブツ)に関する規格です。スクラッチナンバーは、管理された照明条件下での被検光学面上の引っかき傷の大きさを参照基準のスクラッチナンバーと比較することによって決定されます。そのため、スクラッチナンバーは、実際の引っかき傷の大きさを定量的に表わしているわけではなく、MIL規格に基づいて製作された参照基準のスクラッチナンバーとの比較によって決定される、いわば定性的なスペックと言えます。これに対し、ディグナンバーは、被検光学面上のブツ (小さなくぼみ)の実際の大きさに直接関係しています。ディグナンバーは、くぼみの大きさの直径をミクロン単位で表わし、更にそれを10で割った値と同じになります。80-50のスペックは標準品質グレードとして一般的に考えられる仕様なのに対し、60-40は精密グレード、20-10は高精密グレードと考えられます。表面品質に関するより詳細な情報はこちらをご覧ください。
平面度
平面度は、ミラーやウインドウ、プリズムやレンズの平面側に対して、理想的な平面からのそれ量の大きさを表す、面精度に関する仕様の一つです。このそれ量は、オプティカルフラットと呼ばれる高品質で非常に精密な平面参照板を用いることで測定できます。被検光学平面をオプティカルフラットに重ねると、同面の平面度が干渉縞となって現れ、その縞の形状から平面度の大きさを理解することができます。互いの縞が均等かつ真っ直ぐで平行に現れる場合、被検光学平面は参照オプティカルフラットの平面度と少なくとも同じと言えます。縞がもし曲がって現れるようなら、二本の架空上の線を想像します。一本は干渉縞の中央部に引いた接線、他方は同じ干渉縞の末端部間を結んだ線です。この架空上の線が何本できるかで、平面度を求めることができます。平面度の大きさは、使用光源の波長 (λ)の倍数で表わすこともよくあります。干渉縞1本分が半波長 (λ/2)に相当します。一般的に、1λの平面度を持つ平面光学部品は標準品質グレード、λ/4の平面度は精密グレード、λ/20の平面度は高精密グレードと考えられています。
パワー
面精度に関する仕様の一つであるパワーは、曲面状の光学面、即ち光学的パワーを持つ光学面に適用されます。平面度を測定する時と同様の手法でその大きさを測定しますが、オプティカルフラットを用いるのではなく、被検曲面と同じ曲率半径を持つように正確に較正された参照曲面 (ニュートン原器)を用いて干渉縞を表示させます。重ね合わせた二つの曲面間のエアギャップにより引き起こされる同様の干渉原理を用いており、被検光学曲面の参照曲面からのそれ量が干渉縞のパターンとなって現れます (Figure 6)。参照曲面からのそれ量は、「ニュートンリング」として知られる同心円状リングパターンとなって現れます。リングの本数が多くなるほど、参照曲面からのそれ量が大きくなります。暗いリングまたは明るいリングの総本数 (明るいリングと暗いリングの両方の和ではない) が、波長的誤差の2倍分に相当します。
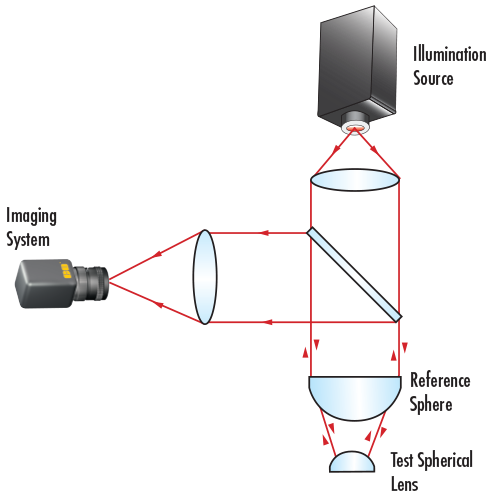
Figure 6: パワーの誤差は参照面との比較や干渉計を用いてテストされる
パワーの誤差は、曲率半径上の誤差に相当し、以下の公式によってその大きさが表されます。ここで、∆Rは曲率誤差、Dはレンズ径、Rは対象曲面の半径、λは波長になります (通常は632.8nm):
イレギュラリティ
イレギュラリティは、被検光学面の形状が参照面の形状からどのようにそれているかを規定する面精度に関する仕様の一つです。パワーを測定するのと同じ手法で干渉縞を得ます。イレギュラリティの反対語であるレギュラリティは、参照面に対して得られる被検光学面の干渉縞パターンが円形状になる時の状態です。ニュートンリングの本数が5本よりも多くなると、1本に満たない本数のイレギュラリティを見つけ出すことが難しくなります。そのため、面精度の仕様を規格化する際は、パワーとイレギュラリティの比率をおおよそ5:1の比にすることが慣習として行われています。オプティカルフラットや平面度、パワー、イレギュラリティといった面精度をテストする際の干渉縞パターンの評価法に関するより詳細な情報は、オプティカルフラットのページをご覧ください。
面粗さ
表面仕上げとしても知られる面粗さは、面上の小規模なイレギュラリティを差します。残念ながら、面粗さは研磨工程の副産物と言えます。粗い表面は、スムーズな表面よりも早く浸食する傾向にあるため、レーザー光や強い熱がこの部位に照射されると核生成現象によって小さなひび割れや欠陥を引き起こす可能性があり、一部のアプリケーションには適さない場合も出てきます。面粗さに対する製造公差範囲は、標準品質レベルの50Å RMSから精密品質の20Å RMS、そして高品質の5Å RMSまでが一般的です。
材料上の仕様
屈折率
媒質の屈折率は、媒質中における光速に対する真空中の光速の比となります。ガラスの代表的な屈折率は、1.4 ~4.0の範囲にあり、可視光を透過するガラスは、赤外透過材料よりも屈折率が低いのが一般的です。例えば、N-BK7 (最も汎用的な可視光透過ガラス)の屈折率は1.517なのに対し、ゲルマニウム (汎用的な赤外透過結晶)の屈折率は4.003です。赤外透過材料に関する更なる情報は、赤外 (IR) アプリケーションで使用する正しい材料をご覧ください。光学ガラスの屈折率は、光学面における光学的なパワーが面の曲率半径と入射/出射時の媒質間の屈折率差の両方によって引き起こされることから、重要な特性となります。光学ガラスメーカーによって規定されるガラスの均質性は、ガラス内での屈折率のばらつきを表します。屈折率の均質性は等級によって異なり、等級が上がると均質性は高くなります – 言い方を変えれば、等級が上がると屈折率のばらつきは少なくなります (Table 3)。
Table 3: 光学ガラスの均質性 | |
---|---|
等級 | 屈折率の最大ばらつき |
0 | +/- 50 x 10-6 |
1 | +/- 20 x 10-6 |
2 | +/- 5 x 10-6 |
3 | +/- 2 x 10-6 |
4 | +/- 1 x 10-6 |
5 | +/- 0.5 x 10-6 |
アッベ数
ガラスの材料に関する他の特性にアッベ数があります。アッベ数は、ガラスによって生じる分散の大きさを定量化したものです。材料のF線 (486.1nm)、d線 (587.6nm)及びC線 (656.3nm)における屈折率の関数となります (下記公式 (3)を参照)。
アッベ数の代表的な数値は25~65の範囲にあります。アッベ数が55を超えるガラスは、分散が少なく、クラウンガラスと呼ばれ、50よりも少ないガラスは、分散が大きく、フリントガラスと呼ばれます。分散が原因で、ガラスの屈折率は波長によって変化します。このことで最も理解しておかなければならない点は、光の波長が変わると、少しずれた位置に焦点を結んでしまうという事実です。屈折率やアッベ数といった材料に関する重要な仕様に関してより詳細な情報が必要な場合は、光学ガラスのページをご覧ください。
レーザー耐力
レーザー耐力は、レーザー光入射時に光学面が損傷を受けずにどこまで耐えられるかを表す単位面積当たりの最大入射光量を差します。数値は、パルスレーザーと連続波 (Continuous Wave; CW)レーザーの両方またはどちらかで規定されます。レーザー耐力は、特にミラーにとって大変重要な材料上の仕様になります。他の光学部品に比べて、レーザー製品と組み合わせて用いられることが多いためです。しかしながら、他の光学部品でもそれがレーザーグレード用のものであれば、この特性が規定されていることが一般的です。一例として、0.5 J/cm2 (@ 150 fs パルス)と100kW/cm2 (@ CW)のレーザー耐力特性を持つチタンサファイアレーザーミラーを考えてみます。このミラーは、高い繰り返しショット数を有するフェムト秒パルスレーザーからは1平方センチメートル当たり0.5J、また高出力CWレーザーからは1平方センチメートル当たり100kWのエネルギー密度に耐えることができることを意味しています。レーザー光がより小さい面積内に集光される場合は、エネルギー密度がこのスペック値を超えないように適切に配慮されなければなりません。
製造上、外観上、及び材料上のその他の仕様も含め、最も共通した光学的仕様を理解すれば、悩みをかなりなくすことができます。レンズ、ミラー、ウインドウ、フィルター、偏光素子、プリズム、ビームスプリッター、回折格子、ファイバーオプティクスといった各種光学部品は、様々な仕様を共有します。そのため、それらの部品が互いにどう関連し、システムの全体性能にどのような影響を及ぼすのかの理解が持てれば、オプティクスやイメージング、或いはフォトニクスアプリケーション内にどの部品を実装するのが最良なのかの選定作業も容易になります。
もしくは 現地オフィス一覧をご覧ください
クイック見積りツール
商品コードを入力して開始しましょう
Copyright 2023, エドモンド・オプティクス・ジャパン株式会社
[東京オフィス] 〒113-0021 東京都文京区本駒込2-29-24 パシフィックスクエア千石 4F
[秋田工場] 〒012-0801 秋田県湯沢市岩崎字壇ノ上3番地